1. Working principle of polarizer
Polarizer is called polarizer, which can control the polarization direction of a specific beam. When the natural light passes through the polarizer, the light whose vibration direction is perpendicular to the passing axis of the polarizer will be absorbed. Only the polarized light whose vibration direction is parallel to the passing axis of the polarizer will be absorbed.
There are two polarizers attached to both sides of the glass substrate in the liquid crystal display module. The lower polarizer is used to convert the light generated by the back light source into polarized light, and the upper polarizer is used to analyze the polarized light after the liquid crystal electric modulation, so as to generate the light and dark contrast, so as to generate the display screen. The imaging of LCD module must rely on polarized light. Without any polarizer, the LCD module cannot display the image.
The basic structure of LCD module is shown in the figure below:
2. Basic structure of polarizer
Polarizers are mainly made of PVA film, TAC film, protective film, release film and pressure-sensitive adhesive. The basic structure of the polarizer is shown in the figure below:
Basic structure of polarizer
PVA film is the core material of polarizer. PVA film adsorbs iodine molecules with two-way absorption function after dyeing. Iodine molecules are arranged orderly on PVA film by stretching, forming polarized light film with uniform two-way absorption performance, whose transmission axis is perpendicular to the stretching direction.
The characteristics and functions of the main membrane materials that make up the polarizer are shown in the table below:
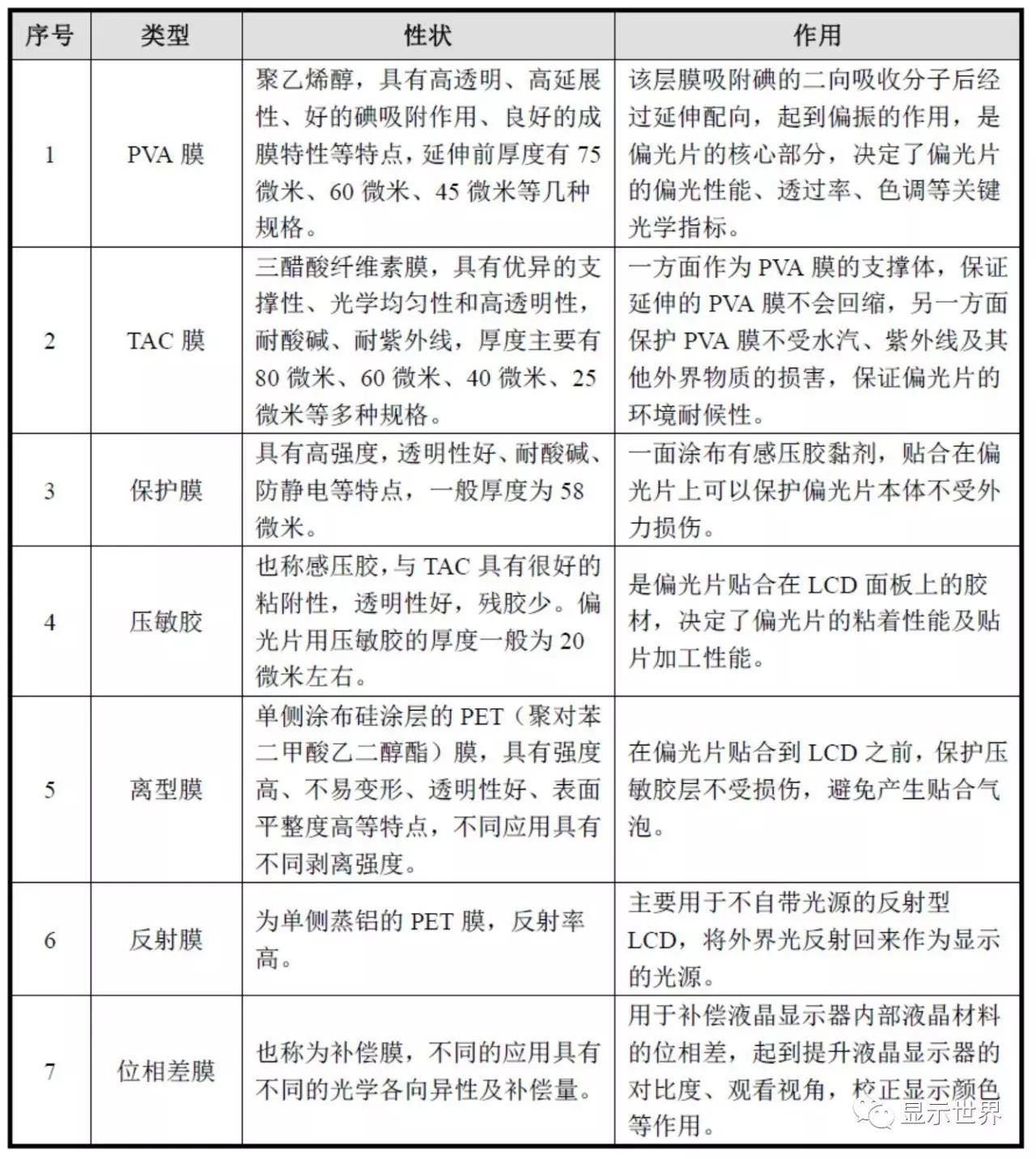
LCD panel characteristics are closely related to polarizer quality
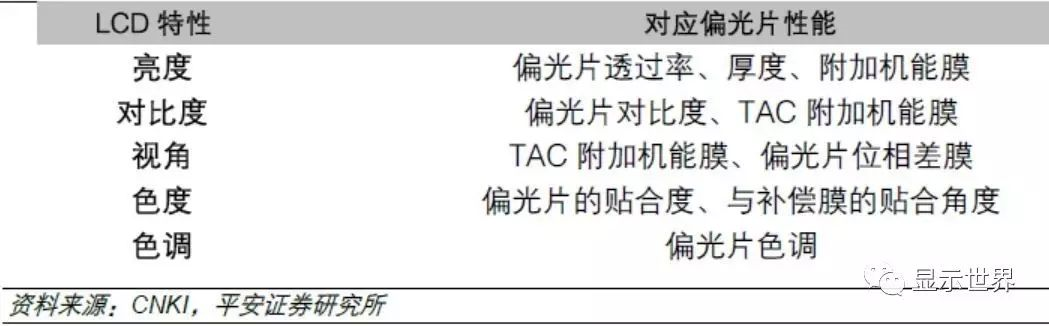
In terms of value distribution, PVA membrane and TAC membrane account for the highest cost of raw materials of all polarizers, of which TAC membrane accounts for about 50% and PVA membrane accounts for about 12%.
Polarizers in the whole display industry chain, the profit is better.
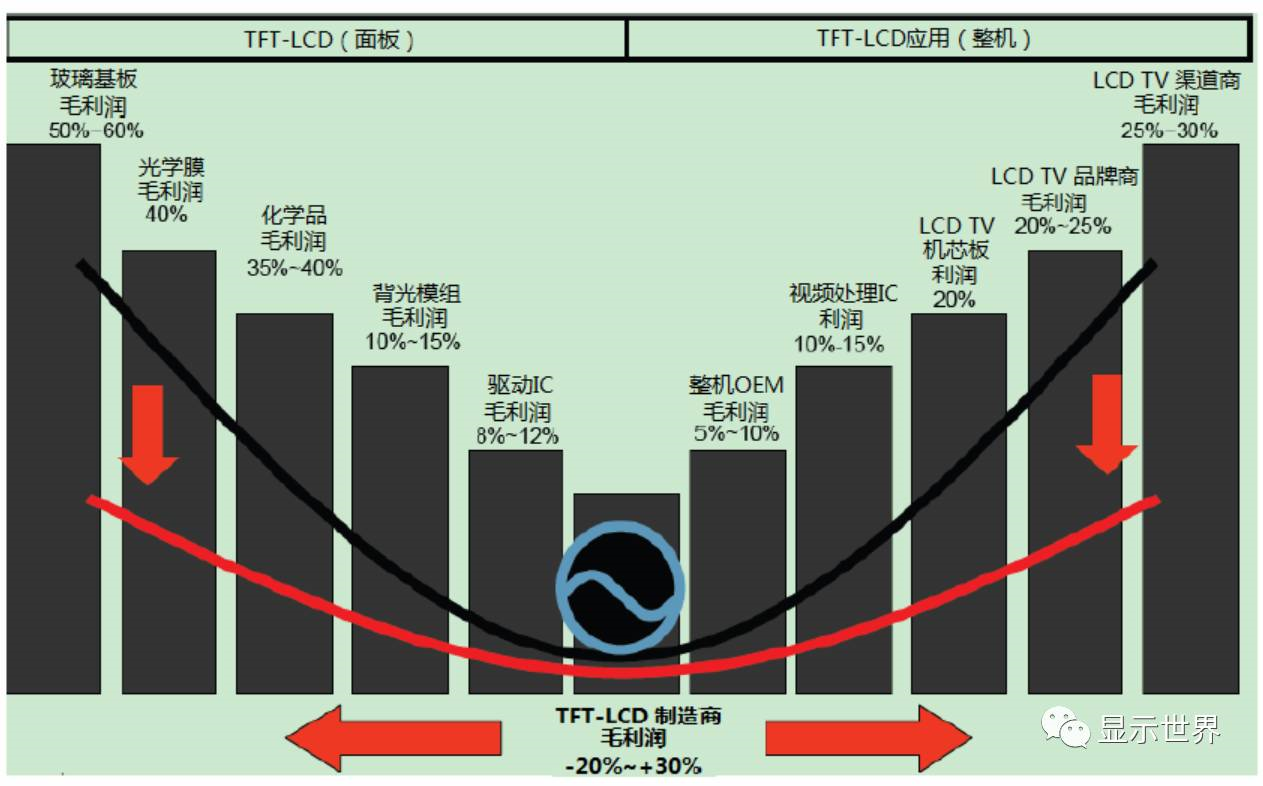
PVA film is the core material to realize polarization function
PVA (polyvinyl alcohol) film is called polyvinyl alcohol film. Its components are mainly light atoms such as carbon, hydrogen and oxygen, so it has the characteristics of high light transmittance and high ductility. When PVA membrane is dyed in a dye bath, a layer of iodine molecules (or dye molecules) will be uniformly enriched on its surface. The untreated PVA molecular chain is disorderly distributed, and the iodine molecule (or dye molecule) adsorbed on it is also disorderly distributed; when PVA is stretched by external force, the PVA molecular chain is distributed in the direction of external force, and the iodine molecule (or dye molecule) is also orderly distributed, so that PVA film has the function of polarization.
The ordered distribution of PVA molecular chain in PVA film after stretching
The stretching of PVA film and the arrangement of iodine molecules are as follows:
There are parallel gaps between the parallel iodine molecules (or dye molecules). These gaps will allow the beams with the same polarization direction as the arrangement direction of iodine molecules (or dye molecules) to pass through, and prevent the beams with other polarization direction from passing through, that is to say, non polarized light is filtered into polarized light.
Non polarized light is filtered as polarized light after passing through the gap of iodine molecules (or dye molecules) in directional arrangement
At present, the polarizers on the market can be classified according to the different dichroic molecules which play the role of polarizing on PVA film, mainly including metal polarizing film, iodine polarizing film, dye polarizing film and polyethylene polarizing film. Because of the high transmittance and degree of polarization, iodine based polarizing film is widely used at present.
Extending PVA film is the core step in the production of polarizer. According to the different methods of extending PVA film, the production of polarizer can be divided into two categories, i.e. dry manufacturing and wet manufacturing. Among them, the dry method refers to the PVA membrane extension in a certain temperature of steam environment, while the wet method refers to the PVA membrane extension in a certain proportion of liquid. The PVA film obtained by wet process has good uniformity and durability, which is the production mode adopted by most polarizer manufacturers at present.
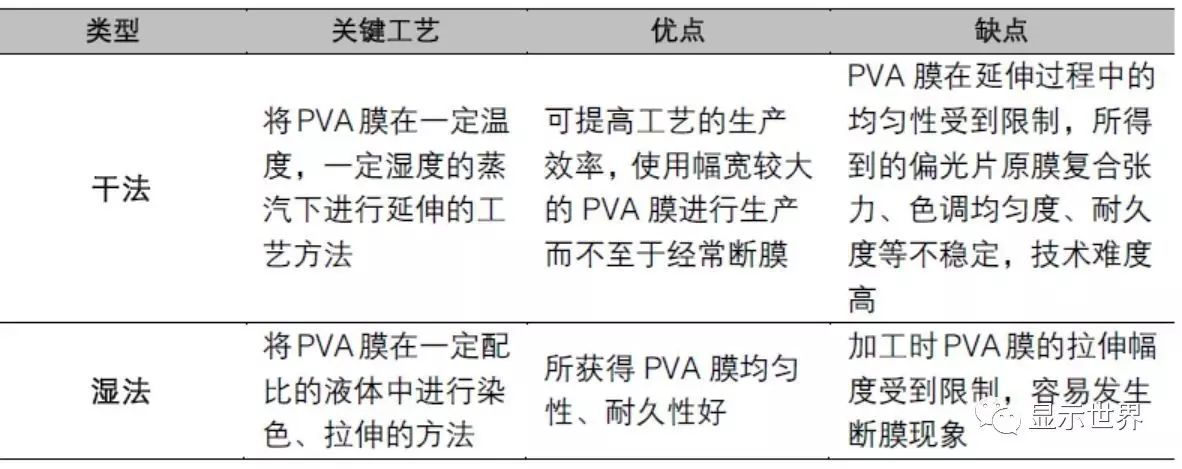
In the finished polarizer, the area of polarizer is equal to the area of PVA film in theory. In the process of polarizer manufacturing, PVA membrane pretreatment must be extended, so the actual production of polarizer consumes about 0. 5 M2 PVA membrane.
At present, China's PVA membrane market is mainly monopolized by Japan cola, and cola itself is one of the main suppliers of high-end PVA resin raw materials in the world. Colly's monopoly in the field of PVA optical film also benefits from its integrated production system, which can realize the integrated production from high-end PVA resin, to the production of PVA film for polarizer, to the surface treatment of PVA film. According to kolli data, at present, the supply of kolli PVA resin accounts for about 40% of the global supply, and the supply of PVA film for polarizer accounts for 80% of the global supply.
Irreplaceable raw material, TAC membrane
TAC (triacetate & nbsp; cellulose) membrane is triacetate fiber membrane, which is obtained by dissolving, filtering, plasticizing, injection molding, drying and other processes of powder TAC particles. It has excellent light uniformity, transparency, acid and alkali resistance and UV resistance.
TAC membrane preparation process
The quality of TAC film used in polarizer production is very high. It is required to control all kinds of parameters in the production process so that the final product can achieve high flatness, excellent mechanical properties and optical properties. The whole production process has a very high demand for process control ability. At present, the commonly used TAC film thickness specifications on the market are 40 & mu; m, 50 & mu; m, 57 & mu; m, 80 & mu; m, among which 50 & mu; m and 80 & mu; m are the most mainstream.
The TAC films used in polarizer production can be roughly divided into two categories, i.e. optical plate TAC films (applied to the inner layer of Polarizer) and TAC functional films (applied to the outer layer of Polarizer). Among them, the light plate TAC film refers to the TAC base film without any surface treatment or additional film layer, and the TAC functional film refers to the TAC film with different functions after being treated by coating, sputtering and other surface treatment methods.
According to the final use purpose, common surface treatment methods include: anti glare treatment (Ag), anti glare + low reflection treatment (Ag + LR), transparent hardening + low reflection treatment (CHC + LR), transparent hardening treatment (CHC), anti reflection treatment (AR), etc. Different surface treatment methods can meet the application requirements of different terminals, for example, CHC processing is mostly used for touchable mobile electronic devices. At present, the surface treatment has been widely used in all kinds of electronic products.
Different application terminals need different surface treatment methods
In essence, most of the above surface treatment is to add a layer of functional film on the original TAC film. For example, AR processing is to coat a layer of material on the surface of TAC film, so that the incident light and the reflected light are offset due to mutual interference, so as to eliminate reflection; Ag processing is to over concentrate the light, and to coat a layer of uneven film on the surface of TAC film of optical plate, so that the light is more dispersed.
Ar processing eliminates the interference between incident light and reflected light
After AG treatment, there is even light coming into view from different angles
For each LCD panel, two polarizers are required, and each polarizer requires two TAC films, that is, four TAC films are required for each LCD panel, while TAC functional films are often only used for the outermost layer.
Most of the TAC film suppliers supply both the TAC film and the TAC functional film, such as Fujifilm, Konica Minolta, paper making in Japan, new optical synthetic fiber in Taiwan, Xiaoxing in South Korea, etc.; some enterprises also purchase the TAC film for surface treatment and processing, such as Japan printing, Toppan Printing, lindko, Dongshan in Japan, etc. In addition, there are also some polarizer manufacturers, such as LG Chemical, Ridong electric, etc., which have the ability of surface treatment of TAC film, and can meet some of their own needs.
The surface treatment of TAC can be completed by TAC manufacturer, coating company and polarizer manufacturer
Although TAC film manufacturers, coating enterprises and polarizer manufacturers all have certain TAC film surface treatment technology and ability, but the technical advantages of different enterprises are different. For example, Japanese printing is the industry leader of high-definition anti glare Ag film, accounting for more than 70% of the market of Ag film; letterpress and Japanese paper are good at CHC processing, and letterpress is the leader of dry production of AR film. Some polarizers, such as LG Chemical, can produce Ag films, but other types of surface treatment capabilities need to be developed. But for example, Li te optoelectronics, Shengbo optoelectronics and Sanli spectrum have not mastered TAC membrane surface treatment technology. The diffusion of surface treatment technology is slow even in the industry, so enterprises with different TAC membrane treatment technology have a certain market.
Different enterprises have different advantages in TAC membrane surface treatment technology
TAC membrane cleaning and PVA membrane extending and compounding are the core steps of polarizer production
Iodine production technology and wet drawing process
Previous process (TAC membrane cleaning and PVA membrane extension and compounding)
The former process includes the pretreatment of TAC membrane and the extension and compounding of PVA membrane. The pretreatment process of TAC membrane is to treat the alkali solution of TAC membrane, after cleaning the residual alkali solution in water washing tank, dry and rewind. The main purpose of this process is to reduce the contact angle of TAC membrane and facilitate the adhesion with PVA membrane. The details are as follows:
The process of PVA membrane extension and composite is to immerse the PVA membrane after pure water swelling into the dye tank, absorb the iodine molecules absorbed in two directions, then stretch and orient the iodine molecules through the extension tank, and composite the PVA membrane with the TAC membrane after two pretreatment layers after drying to obtain the polarized light membrane. The details are as follows:
Middle process (coating and compound productionProduction line)
The middle process is the process of coating pressure-sensitive adhesive, composite release film and other film materials. In this process, the pressure-sensitive adhesive is coated on the release film, the moisture in the pressure-sensitive adhesive is evaporated through the oven, then it is combined with the polarizing film produced in the previous process, and then it is rolled up, and then it is placed in the constant temperature curing room for curing. Sometimes, due to different product types, other related optical films need to be compounded. The details are as follows:

Post process (cutting production line)
Cut, grind, clean, inspect and package the cured polarizer according to the required size.
The details are as follows:
3. Main product features and application fields
The main performance indexes of polarizer include optical properties, mechanical properties and reliability. The optical properties mainly refer to the transmittance, polarization and hue of the polarizer; the mechanical properties mainly include the warpage of the polarizer and the bonding strength of the pressure-sensitive adhesive of the polarizer; the reliability is the index to measure the durability of the polarizer. The evaluation method is to place the polarizer in the high temperature, low temperature, high temperature and high humidity environment test box for a certain period of timeCheck the change of appearance and optical performance.
The polarizer industry chain is shown in the figure below:
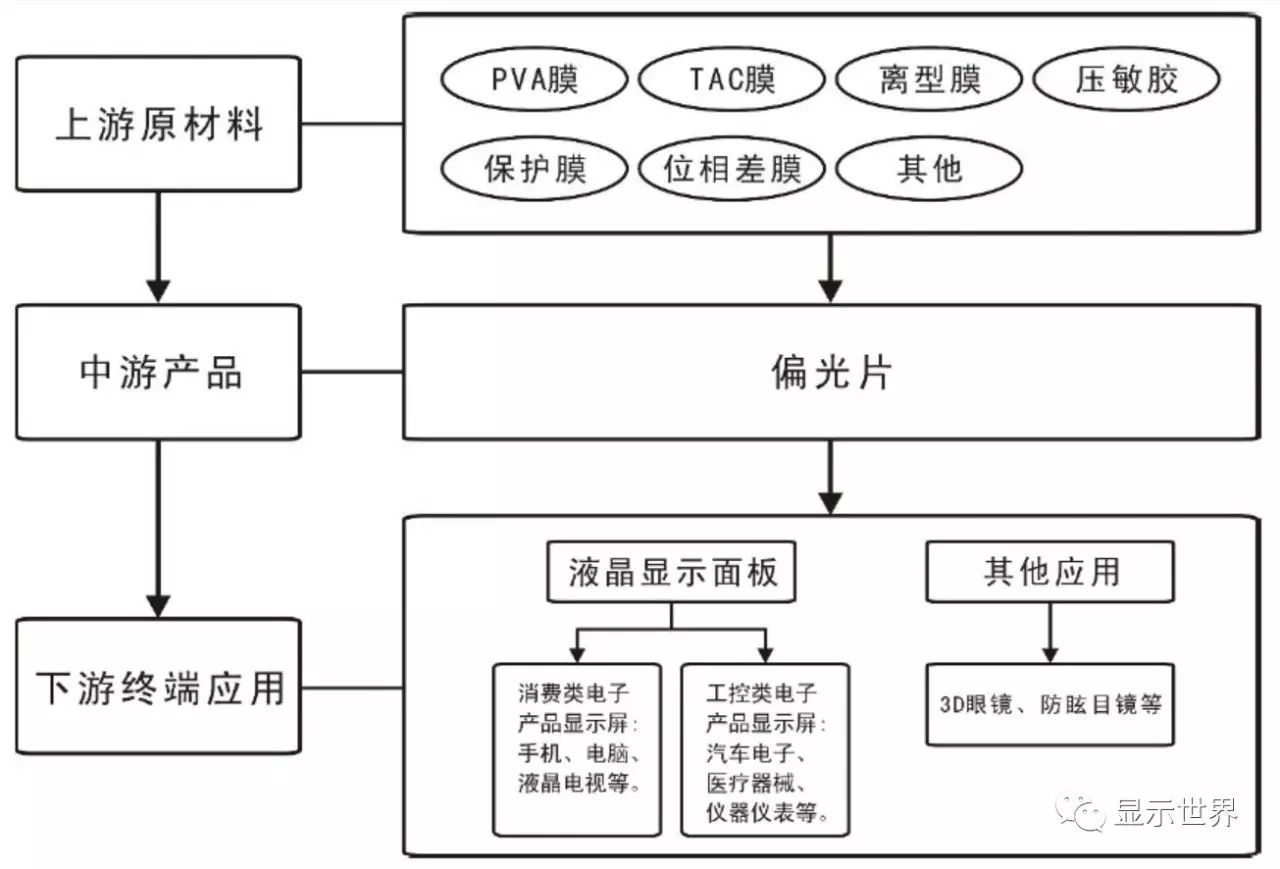
Display the world's comprehensive self: three profit spectrum information, CNKI, Ping An Securities, etc